METERING WITH ECOGEAR PUMP
When a plant engineer is required to select and specify a chemical metering pump, the decision is often regarded as a simple choice between a reciprocating plunger pump or a diaphragm pump and gear pumps are seldom even considered. This understanding has evolved over the years until the terms metering and reciprocating pump have nearly become synonymous. Conventional Metering Pumps, whether reciprocating plunger or diaphragm (disk or tubular shape), operate on the same common principle. The volume of the pumping chamber is altered by the reciprocating action, which changes the pressure exerted on the fluid being pumped. The pumping action is controlled by a pair of unidirectional check valves, Figure 1.
Displacement is determined by the plunger cross-sectional area, stroke length and cycle rate. In theory, reciprocating pumps displace a constant volume of fluid with each stroke of the plunger. In actual operation, the discharge may vary from the ideal because of erratic action of check valves or variation in the flexing action of the diaphragm during successive pulses. In addition to check valve problems, reciprocating plunger pumps have these limitations: they deliver output in pulses, exhibit poor suction lift, are sensitive to changes in liquid viscosity, and require a complex drive for varying stroke.
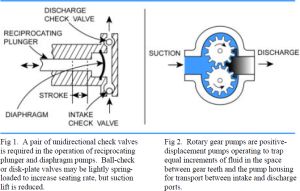
Displacement is determined by the plunger cross-sectional area, stroke length and cycle rate. In theory, reciprocating pumps displace a constant volume of fluid with each stroke of the plunger. In actual operation, the discharge may vary from the ideal because of erratic action of check valves or variation in the flexing action of the diaphragm during successive pulses. In addition to check valve problems, reciprocating plunger pumps have these limitations: they deliver output in pulses, exhibit poor suction lift, are sensitive to changes in liquid viscosity, and require a complex drive for varying stroke.
Reciprocating plunger pumps usually require a flooded suction for optimum service. They are essentially pressure intensifiers and exhibit poor suction lift characteristics. An elevated reservoir, a pressurized supply tank, or feed pump may be required with liquids that do not flow freely and liquids that have low vapor pressures. Viscosity of the liquid entering the pump may change when the fluid is of an inprocess intermediate nature, or if the temperature changes radically. When viscous liquids must be handled by reciprocating pumps, oversize suction lines and low cycle rates are required to assure that the chamber is completely filled during each stroke. When high capacities are required, the cost of the pump increases accordingly.
The ability to vary the stroke length during operation increases the complexity of the drive design in reciprocating metering pumps. Several methods are available: direct stroke adjustment, eccentric cam adjustment, and lostmotion devices to limit movement of the plunger during a portion of the return stroke.
An Alternative Method – In many applications, specifically when high pressures are required, the reciprocating pump is preferable, if not the only choice. The rotary gear pump is an alternative that should n